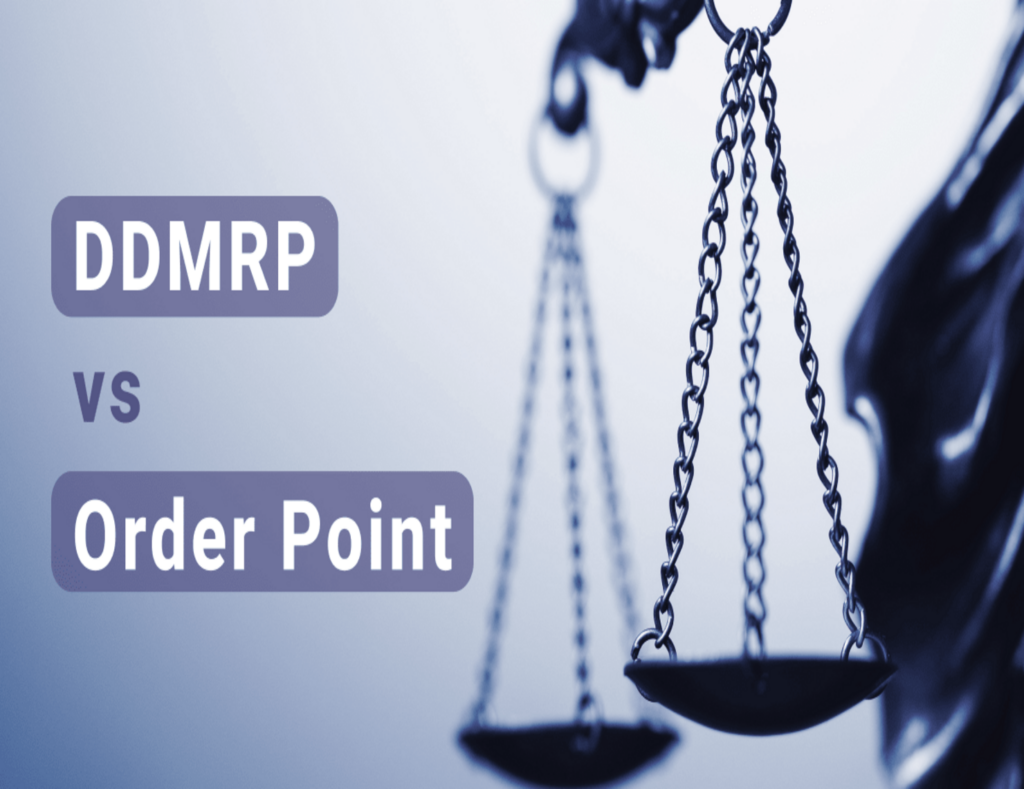
De oorsprong van Order Point
Hoe zag het voorraadbeheer eruit vóór MRP?
Voordat MRP werd ingevoerd, was de meest populaire aanpak van voorraadbeheer: Order Point. De belangrijkste beperkingen hiervan lagen binnen de bedrijven zelf. Dat wil zeggen, de markt wilde vaak meer dan dat een bedrijf daadwerkelijk kon leveren. Alles wat werd geproduceerd kon worden verkocht en zou ook worden verkocht. Daarom was de belangrijkste vraag op welke manier effectief aan de marktvraag voldaan kon worden. Er waren weinig SKU’s in het assortiment, de producten waren niet complex en de levenscyclus van de producten was lang. Soms werden artikelen tientallen jaren zonder enige aanpassing geproduceerd.
Wat betekende dat voor het voorraadbeheer? Bedrijven hadden een paar SKU’s, met een stabiele vraag en BOM (Bill of Material) die een voorspelbare vraag naar componenten creëerden. Deze ongecompliceerde, stabiele, lineaire systemen waren eenvoudig te beheren en te optimaliseren. Toen ontstond het concept van EOQ (Economic Order Quantity -Economische orderhoeveelheid-), dat onderdeel werd van het Order Point systeem.
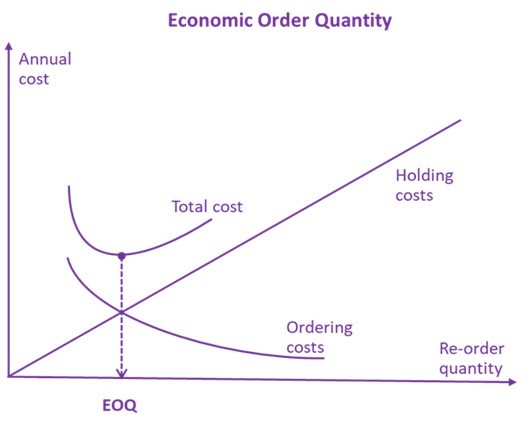
Economische orderhoeveelheid (EOQ) leren begrijpen
Als we aannemen dat de vraag, de bestellings- en de voorraadkosten bekend zijn en niet veranderen over een bepaalde periode (meestal een jaar), kan het punt berekend worden waarop de totale voorraadkosten tot een minimum worden beperkt. Dat is de logica achter de klassieke versie van EOQ. Moderne EOQ-systemen gebruiken gewoonlijk complexere formule-uitbreidingen die meer variabelen aan de vergelijking toevoegen. Maar de oorspronkelijke veronderstelling -dat vraag en kosten bekend zijn en niet veranderen- blijft gelden.
In de wereld van VUCA neemt het aantal SKU’s in het assortiment, het product en de complexiteit van de toeleveringsketen toe, terwijl de levenscycli van producten korter worden en de vraag van klanten allesbehalve bekend en stabiel is. Helaas gebruiken we dus formules voor een wereld die niet meer bestaat. Gewoonlijk leidt de toepassing van de EOQ-logica in moderne productiebedrijven tot grotere productiebatches, waardoor een bedrijf zijn productiecapaciteit en materialen verkeerd gebruikt. De meest voorkomende resultaten zijn een hogere OOE (overall operations effectiveness), een minder flexibele productieplanning en hogere voorraadniveaus.
Het goede nieuws? Na een typisch EOQ-project is er ruimte voor verbetering met DDMRP. (Lees hoe Kormotech van de implementatie van EOQ is overgestapt op DDMRP).
Maar laten we eerst eens kijken hoe Order Point en EOQ werken.
EOQ en Order Point
Hoe werkt Order Point? De figuur hieronder toont de EOQ en het Order Point. Het idee is eenvoudig. Wanneer het totale voorraadniveau, plus de artikelen die “in bestelling” staan, een bepaald niveau bereiken, wordt een nieuwe leveringsorder gegenereerd. Hoeveel moeten we bestellen? Kijk naar de EOQ.
Hoe wordt het Order Point berekend? Dit is gewoonlijk het verbruik over de doorlooptijd plus het niveau van de veiligheidsvoorraad. De partij kan dus worden geleverd, voordat de veiligheidsvoorraad is verbruikt, als we ervan uitgaan dat er geen variabiliteit is in vraag of aanbod (punt 2).
In de realiteit zal de vraag van de klant altijd hoger of lager zijn dan verwacht (punten 1 en 3) of kan de leverancier/productie vertraging opleveren (punt 4). Het is de taak van de veiligheidsvoorraad om dergelijke schommelingen op te vangen.
Nogmaals, omdat het zo eenvoudig is en het veel lijkt op ‘gezond verstand’, is de aanpak nog steeds vrij populair en wordt deze nog altijd in veel bedrijven gebruikt.
De beperkingen van Order Point
Vaste Order Points en veiligheidsvoorraden zijn goed voor lineaire, stabiele en voorspelbare omgevingen. Maar hoeveel zijn er dat tegenwoordig nog? Het resultaat is een bimodale voorraadverdeling (te weinig van het goede en te veel van het verkeerde) en in het algemeen een te grote voorraad.
Normaliter wordt de bimodale voorraadverdeling in deze benadering veroorzaakt door:
- Geen verband met capaciteit. Ook al wordt deze in sommige gevallen berekend, het wordt voor een lange periode vastgesteld en het heeft de neiging om tot te grote batches te leiden.
- Assortimentslijst en BOM wijzigingen. Order Points en EOQ’s raken sneller verouderd dan dat ze in de praktijk worden herberekend.
- Hoge promo’s of seizoen gebondenheid ondermijnen de doeltreffendheid van deze aanpak en leiden meestal tot tijdelijke oplossingen.
- Geen gebruik van de werkelijke orders van de klant. Als er geen zichtbaarheid is, daalt het serviceniveau, of moeten bedrijven hun voorraad verhogen om te kunnen compenseren.
- Gebrek aan het kunnen aanpassen aan de voortdurend veranderende behoeften van de klant en de productieplannen.
Het laatste punt was een van de belangrijkste redenen waarom de Order Point-benadering werd vervangen door de MRP-technologie. De naam zegt het al: “Material Requirements Planning”, dat de behoeften rechtstreeks worden her-berekend op basis van het huidige productieplan, met behulp van de materiaallijst.
Hierdoor geloven bedrijven dat zij alleen zullen produceren wat werkelijk nodig is om aan de vraag van de klant te voldoen -en alleen grondstoffen kopen wanneer en in de hoeveelheden die zij nodig hebben om het aan productieschema te voldoen-. Dit zette de deur open voor afhankelijke planning via de materiaallijst, die tot een hogere ROI moest leiden. En dat deed het ook, toentertijd. Maar hoe veranderlijker en onvoorspelbaarder de omgeving wordt, hoe minder efficiënt MRP wordt. Maar dat is weer een ander verhaal.
Hoe DDMRP-buffers kunnen helpen
DDMRP-buffers zijn gebaseerd op een mechanisme dat vergelijkbaar is met re-order points. Echter corrigeren ze hun beperkingen, zodat ze efficiënter zijn in een meer variabele wereld: dynamische aanpassing van niveaus, lettend op relevante eisen van klanten, visueel beheer, rekening houdend met BOM-koppelingen, enz. De DDMRP-buffers van Intuiflow gaan nóg verder door kunstmatige intelligentie, dynamische aanpassing op meerdere niveaus en door implementatie van capaciteitsbeperkingen. Dit alles voor een flexibele en veerkrachtige planning in de wereld van VUCA.