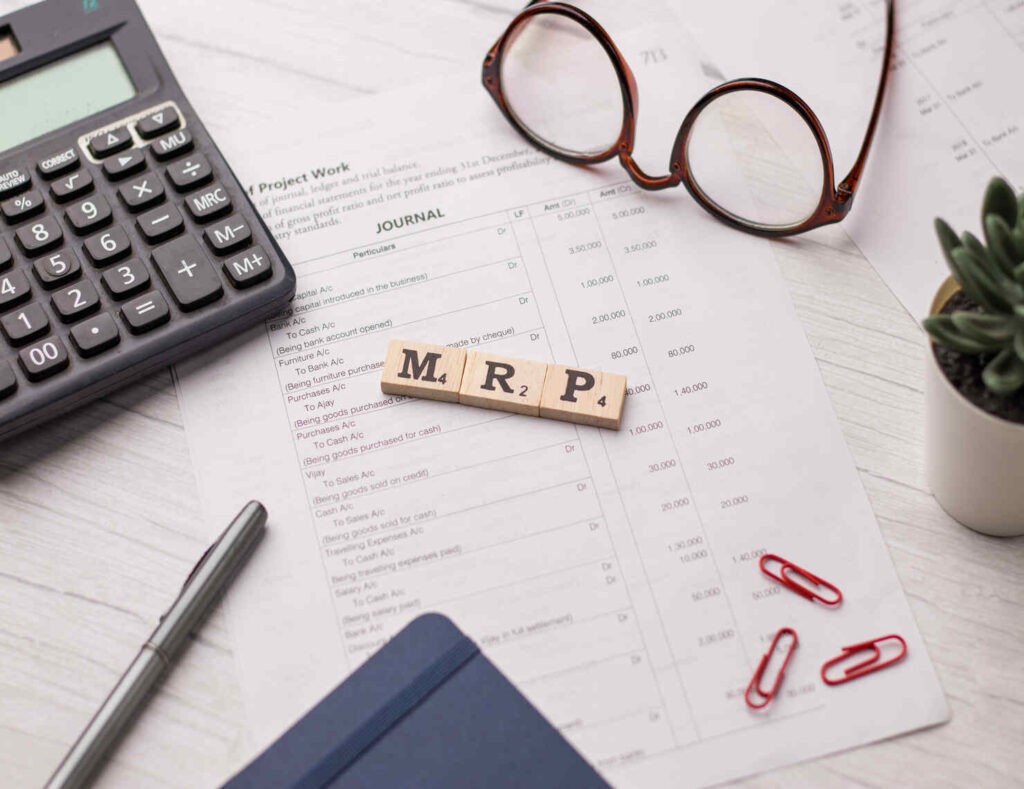
Vóórdat MRP zijn intrede deed, was de meest populaire benadering van voorraadbeheer: Order Point, waarbij elk punt onafhankelijk is. Maar hoe complexer een operationele omgeving wordt -vanwege een langere SKU(Stock Keeping Unit)-lijst of veranderingen in het assortiment en van de vraag- hoe groter de kans op een bimodale voorraadverdeling, waarbij te weinig van de juiste en te veel van de verkeerde voorraden voorhanden zijn. En ook te veel totale voorraad om het gebrek aan aanpassingsvermogen te compenseren.
Het is dan ook niet verwonderlijk dat MRP, dat de deur opende naar afhankelijke planning, al snel de meest gebruikte voorraadbeheerbenadering werd.
De logica achter MRP is heel eenvoudig. Eerst maakt u een verkoopprognose, die planners gewoonlijk uit het S&OP-proces halen. Zodra u “weet” (d.w.z. kunt voorspellen) hoeveel en wanneer u gaat verkopen en u de foutmarge van de voorspelling begrijpt, is het niet moeilijk om te uit te rekenen hoeveel voorraad u moet aanhouden om de verwachte verkoop voor elk SKU te kunnen dekken. De meeste bedrijven beschikken over actuele voorraadgegevens en WIP (Work in Progress – onderhanden werk). Uitgaande van hoeveel er wanneer nodig is, vergeleken met hoeveel er beschikbaar is, is het verschil tussen beide een vereiste voor de productie.
Maar in de dagelijkse praktijk ligt het iets gecompliceerder. Er is meer dan één SKU en er zijn bepaalde materiaalvereisten. Hierdoor moeten planners het werk in een bepaalde volgorde plannen, niet alleen om aan de vraag te voldoen, maar ook om “operationeel efficiënt” te zijn (wat gewoonlijk betekent dat de kosten worden geminimaliseerd door het verhogen van de productiebatches). Wanneer het werk in exacte hoeveelheden en timing is gepland, is het gemakkelijk om de materiaalvereisten te berekenen via de BOM (Bill of Material). Daarom wordt het ‘afhankelijke planning’ genoemd. Afhankelijke planning is een systeem dat leveringsorders genereert voor de dekking van het productieschema, enkel op basis van de hoeveelheid benodigde componenten en wanneer deze nodig zijn.
We overlopen de APICS definitie van MRP:
“Een reeks technieken die gebruik maakt van materiaallijstgegevens, voorraadgegevens en het hoofdproductieschema om de materiaalvereisten te berekenen. Het doet aanbevelingen om aanvullingsorders voor materiaal vrij te geven. Bovendien, omdat het tijd gefaseerd is, doet het aanbevelingen om open orders te herschikken wanneer vervaldatums en behoefte-datums niet gefaseerd zijn. Time-phased MRP begint met de artikelen die op de MPS staan en bepaalt (1) de hoeveelheid van alle componenten en materialen die nodig zijn om de artikelen te fabriceren en (2) de datum waarop de componenten en materialen klaar moeten zijn. Time-phased MRP wordt bereikt door de materiaallijst aan te passen voor voorraadhoeveelheden -in de voorraad of in de bestelling- en de netto-vereisten te compenseren met de gepaste doorlooptijden. – APICS Woordenboek
In de onderstaande diagrammen ziet u een eenvoudige weergave van de Bill of Material-structuur, samen met de benodigde apparatuur om materialen om te zetten naar afgewerkte producten en in welke volgorde en binnen welke tijdsspanne. Het icoon met drie vakjes betekent: opgeslagen materialen of afgewerkte producten, afhankelijk van het niveau van de BOM. Elke rechthoek vertegenwoordigt een SKU in de BOM, terwijl een cirkel met een nummer staat voor een specifiek onderdeel van de productieapparatuur. Zoals u ziet, hebben we 30 dagen nodig om een afgewerkt product A te maken en 14 dagen voor product B.
Omdat de leverings- en productiedoorlooptijden langer zijn dan de tolerantietijden van de klant, moet het bedrijf over die periode plannen. S&OP en het opnieuw berekenen van prognoses kosten veel tijd en energie. Bovendien krijgt het bedrijf na elke MRP-run een nieuw resultaat dat in tegenspraak is met het vorige. Dat brengt iedereen in verwarring, vooral de mensen op de werkvloer die het fysiek zouden moeten uitvoeren. In een poging dat systeem te stabiliseren, wordt de productieplanning gewoonlijk maandelijks gemaakt, één of twee maanden in voren.
De maandelijkse planning stelt bedrijven in staat hun beheerssystemen te vereenvoudigen, waardoor de planning een belangrijk managementinstrument wordt. Hierdoor is eenvoudig te zien of de verkoopafdeling meer of minder heeft verkocht dan gepland en of de operationele afdeling volgens plan heeft geproduceerd of juist niet.
In de afbeelding hieronder ziet u een eenvoudige visualisatie van een voorbeeld van een MPS (Master Production Schedule). Elke dag worden het nummer en het volume van een specifieke SKU in volgorde van planning ingegeven voor de productie. Ook hier -gebruikmakend van hun doorlooptijden en BOM- om de vereisten voor producten A en B te berekenen, waardoor de materiaalvereisten berekenend kunnen worden.
MPS en MRP zijn prima oplossingen als u 100% betrouwbare leveranciers, apparatuur en materialen heeft én 100% accurate stamgegevens en prognoses. Maar wat gebeurt er als dat niet het geval is?
Waarom productieschema’s een vals gevoel van stabiliteit geven
Stelt u zich voor dat u een planner bent in de fabriek. De nieuwe maand komt eraan, en het managementteam komt op bezoek. Het S&OP proces heeft zowel de verkoop- als de productieplannen goedgekeurd. Door uw ervaring, weet u dat het vaak de verkoopafdeling is die vraagt om het plan aan te passen. Dus vraagt u hen opnieuw: “Is dit de manier waarop u wilt dat de productie verloopt, of moet ik wijzigingen aanbrengen? Realiseert u zich dat alle activiteiten, inclusief het inkopen van materialen, op dit schema worden afgestemd?”
U krijgt altijd hetzelfde, eerlijke antwoord aan het begin van de maand: “Dit is het beste plan, dit moeten we volgen.”
Uw productieplan dekt niet alleen de verwachte verkoop, maar is zo opgesteld dat de doeltreffendheid van uw machines optimaal is en de productiekosten, zoals materiaalverspilling en ongebruikte tijd, tot een minimum worden beperkt. Het is het best mogelijke plan; daar kan intern niemand aan twijfelen. Het management kent een KPI toe, waardoor u gestimuleerd wordt om dit plan perfect uit te voeren. Het enige wat u dus moet doen om een bonus te krijgen -en om het bedrijf succesvol te maken- is u aan het plan houden.
Nu is het de ochtend van dag 7… Het plan voor vandaag is om product N af te maken en product M te lanceren. Het is zeven dagen geleden dat begonnen is met de uitvoering van het schema en voorbereidingen worden getroffen om twee opeenvolgende dagen product O te produceren. Plotseling komt het verzoek van de verkoopafdeling om producten L en K te maken, omdat zojuist een zeer winstgevende order van een klant is binnengekomen. De huidige voorraden zijn niet voldoende om die order te kunnen leveren. Intussen is de verkoop van product O precies volgens planning verlopen en zijn er nog veiligheidsvoorraden. De opties voor dag 8:
- Optie A: Bouw O. We verliezen de verkooporder, extra winst, en waarschijnlijk een klant. Maar volgens onze KPI hebben we het geweldig gedaan, omdat we de planning conform afspraak hebben uitgevoerd. We krijgen onze bonus aan het eind van de maand.
- Optie B: Bouw K en L. We hebben extra werk om de materialen voor te bereiden, meer en andere instellingen in te geven en, uiteraard, een hoger percentage inactieve tijd en meer verspilling van materiaal. Ook een lager percentage van de geplande uitvoering. De planners krijgen hierdoor geen bonus. In plaats daarvan presteert de verkoopafdeling wel beter dan gepland en krijgt dus een bonus.
- Optie C: De planner selecteert optie “B”, maar kan deze niet met succes uitvoeren. MRP behandelt alles als ‘afhankelijk’. Het systeem is niet ontworpen om dat te bouwen wat niet is gepland; er kan ook een gebrek aan materialen of capaciteit zijn. Wat de planner weer terugbrengt bij optie “A”.
Deze situatie legt de basis voor conflicten tussen functies/afdelingen binnen een bedrijf. Planners willen gelijke tred houden met de planning, ze kúnnen of wíllen niet produceren wat verkoop hen vraagt. De werkelijke reden (optie A of C) is in de meeste bedrijven niet goed zichtbaar, wat het interne conflict weer versterkt. Verkoop denkt dat planners alleen geven om hun OOE en het uitvoeren van de planning, maar zij zijn niet in staat om verder te kijken dan alleen de functieomschrijving.
Dit leidt tot twee voor de hand liggende mogelijke oplossingen: vaker dan eens per maand MRP draaien om zich aan te kunnen passen aan marktveranderingen. Of een betere prognose maken om de noodzaak van her-planning te minimaliseren.
Als frequentere runs voor meer onrust op de werkvloer zorgen en materiaalplanning na elke run tegenstrijdige aanbevelingen genereert, wordt een betere voorspelling vaak de hoogste prioriteit van managers die op zoek zijn naar oplossingen. Supply chains worden complexer door wereldwijde inkoop en vraag, langere doorlooptijden en productcomplexiteit, terwijl de variëteit toeneemt en tegelijkertijd de productlevenscycli korter wordt en dat alles vermindert de nauwkeurigheid van voorspellingen. Niet omdat we vergeten zijn hoe we prognoses moeten berekenen. Maar door de onzekerheid, variabiliteit en complexiteit van de omgeving waarin we opereren, is er in de gegevens uit het verleden, gewoon geen antwoord te vinden op de vraag hoe de toekomst eruit zal zien.
Hoe veiligheidsvoorraden de variabiliteit versterken
APICS beschrijft het Bullwhip-effect als volgt: “een extreme opwaartse verandering in een bevoorradingsketen, veroorzaakt door een kleine neerwaartse verandering van de vraag in de bevoorradingsketen. Voorraad kan snel veranderen van ‘nabesteld’ in ‘overtollig’. Dit wordt veroorzaakt door de seriële aard van het doorgeven van orders in de gehele keten, met de onvermijdelijke vertragingen door het verplaatsen van producten in deze keten.”
Wat in deze definitie niet wordt vermeld, is het bi-directionele karakter van het effect. Wegens dit ontbrekende element zijn de meest voorkomende pogingen om het effect te verzachten, pogingen om de nauwkeurigheid van de prognoses en het gebruik van veiligheidsvoorraden te vergroten. Veiligheidsvoorraden zijn gewoonlijk bedoeld om het verschil te dekken tussen wat de verwachte verkoop is en wat in werkelijkheid verkocht wordt. Maar wanneer het voorraadniveau ook maar tot één eenheid onder de ingestelde veiligheidsvoorraad daalt, leidt dit tot herbevoorrading. Met het gebruik van MOQ’s (Minimum Order Quanitity), versterkt dit de variabiliteit en verstoort dit het bullwhip-effect. Het leidt ertoe dat bedrijven te veel voorraad nodig hebben om deze schommelingen op te vangen, of onvoldoende capaciteit hebben om extra voorraad aan te leggen wanneer dat nodig is. Beide opties zijn slecht voor de business.
Hoe vraag gestuurde methodes beter presteren dan MRP-voorraadbeheer
Bedrijven moeten vandaag de dag in staat zijn hun productie voortdurend aan de vraag aan te passen, zonder dat dit ten koste gaat van de operationele efficiëntie. Dit is wat Demand Driven-methodes kunnen bewerkstelligen, door gebruik te maken van een reeks technieken die voorraadbeheer en lange-, middellange- en korte termijn beheer integreren om afdelingen met de neuzen dezelfde kant op te zetten en ze te richten op waar het daadwerkelijk om gaat: klanten bedienen op een winstgevende manier.
Wil je meer weten over hoe anders Demand Driven methodes werken? In onze volgende post leggen we alles uit over DDMRP vs MRP!